This King William homeowner had concerns about moisture in their crawl space. The insulation was beginning to fall and there was mildew and mold growth on the floor joists. The existing 6 mil vapor barrier did not completely cover the ground allowing water vapor from the earth to rise into the crawl space. The open vents allow humid air to flow into the crawl space but don’t allow enough ventilation for it to escape. This has resulted in high relative humidity in the space leading to damage to the insulation as it absorbs the moisture in the air and microbial growth on organic surfaces.
The homeowner wanted to understand their options for returning their crawl space to its original state versus encapsulating the space.
The approach of returning the crawl space to its original state would include cleaning the old vapor barrier, debris, and insulation out of the crawl space. Then we would treat the joists with shockwave antimicrobial to kill the mold and mildew. Then a new 6-mil vapor barrier would be installed and anchored to the ground and R-19 fiberglass bats would be installed between the joists.
This option would remedy the current concern of microbial growth, falling insulation, and a damaged vapor barrier, however, it would not be a long-term solution, and the homeowners would likely be doing this project again within a few years. This approach will not stop moisture from impacting the crawl space environment through open vents or vapor rising from the earth.
The 6-mil will be anchored to the ground, meaning that U shaped stakes will be poked through the liner to help keep it in place. However, a 6-mil liner is about as thick as a trash bag meaning it will rip and tear easily. The anchors not only create additional weak points in the material, but it also means that there are more holes allowing water vapor to rise into the crawl space. It also cannot seal the crawl space from the earth’s moisture because it’s slick surface and fragility don’t allow the material to be sealed to the walls or itself at the seams.
As the crawl space fills with moisture, again, the fiberglass batts will continue to soak up that moisture. The batts will again become damaged by the moisture and begin to delaminate. As the fibers of the material pull away from each other the insulation will begin to drip from the floors. The added weight of the moisture will cause the batts to fall away from the floor and that moisture will be held against the floor joists promoting microbial growth. Leaving the homeowners with the same problems they had before.
The approach of Encapsulating the crawl space also begins with cleaning out the existing materials and treating the mold with Shockwave Antimicrobial. The next step would be to install a heavy-duty vapor barrier. We offered the Homeowners the option of a 10 mil or 20 mil CleanSpace Vapor Barrier. The material is durable enough to be attached and sealed to all crawl space walls, 6 inches above outside grade, wrapped and sealed around all piers and sealed at all seams, without anchors creating holes in the liner. This allows us to completely seal the crawl space from the earth’s moisture.
The next step would be to air seal and insulate the crawl space, this includes sealing all vents, the rim & band, sill plate, and any penetrations through the exterior wall such as plumbing lines. This allows us to stop the outside air carrying moisture from flooding into the crawl space and raising the relative humidity.
We then recommend applying closed-cell Spray Foam to the foundation walls. Insulating the crawl space walls allows us to extend the thermal barrier of the home to the floor of the crawl space. This helps reduce the transfer of heat through the foundation walls, further controlling the crawl space environment. We then insulate and air seal behind the crawl space door with a friction fit, insulated panel. This panel creates an airtight seal, preventing air carrying moisture from leaking in around the crawl space door and suffices the required R-10 of continuous insulation when insulating from the crawl space walls.
Finally, we recommend installing a SaniDry Sedona Dehumidifier. This piece of equipment is designed to remove the moisture in the crawl space and circulate dry air throughout the entire space. With ever dehumidifier, we include a hygrometer. The Hygrometer sensor is placed in the crawl space and transmits humidity and temperature readings to a display unit that the homeowner places in their home. The display unit takes temperature and humidity readings inside the home as well. This allows the homeowner to monitor the conditions of their crawl space.
If the homeowners choose to take this approach, it will allow them to not only repair the current damage to the insulation and vapor barrier as well as address the microbial growth. It also allows them to control the crawl space environment to prevent mold growth from reoccurring and stop the damage moisture causes to the insulation. Beyond these benefits, they will also experience improved indoor air quality, lower energy bills, and warmer floors in the winter.
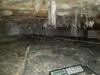